Cubiertas
CAMPOS DE ACTUACIÓN
- Retirada de amianto
- Fibrocemento (uralita)
- Teja (35 años de garantía)
- Metalicas de panel sandwich
- PVC
- Lamina polimerica
- Asilamiento térmico de cubiertas
- Impermeabilización: acrilico, poliuretano y poliurea
- Formación de trasteros
- Proyectado de poliuretano
Retirada de amianto

La comunidad de propietarios debe conocer que, cuando ejecuta obras que afectan a las cubiertas o canalizaciones de fibrocemento que puedan contener amianto, estas deben ser llevadas a cabo siguiendo las medidas preventivas adecuadas de acuerdo con la legislación laboral, y que las empresas que realizan este tipo de trabajos deben estar debidamente autorizadas, esto quiere decir que tienen que estar inscritas en el Registro de empresas con riesgo de amianto (RERA) y tener un plan de trabajo aprobado por la autoridad laboral.
Debido a las graves enfermedades que puede llegar a producir se ha prohibido la comercialización, uso y producción de amianto. En España se prohibido totalmente en el año 2002, pero se permite que los materiales con amianto que estaban instalados con anterioridad se puedan utilizar hasta su eliminación o el final de su vida útil. Esto quiere decir que esos materiales no se pueden reutilizar ni vender aunque estén en buen estado.

Isotec es una empresa inscrita y autorizada por la Xunta de Galicia para la retirada de cubiertas con contenido en amianto. El Real decreto 396/2006, del 31 de marzo, por el que se establecen las disposiciones mínimas de seguridad e salud aplicables a los trabajos con riesgo de exposición al amianto, constituye la norma legal mínima en relación al amianto en nuestro país. En este RD además de recogerse las medidas de protección y prevención que hay que aplicar en estos trabajos con riesgo de exposición, se obliga a las empresas que los ejecutan a realizar diferentes trámites y actuar de la siguiente manera:
- El personal que manipule el desmontaje de las planchas de fibrocemento, así como los depósitos de agua en desuso utilizará un buzo desechable (uno para la jornada de la mañana y otro para la de la tarde), así como guantes desechables y mascarilla de protección.
- Se dispondrá de una caseta homologada de descontaminación con tres compartimentos para colocarse y sacarse el traje de protección de forma segura.
- Las placas de fibrocemento se extraerán sin romperlas y se acopiarán enteras sobre pallets de madera, para ser envueltas en su totalidad en plástico de embalar y flejadas.
- Una vez paletizadas y envueltas, serán recogidas por un contenedor autorizado y trasladadas hasta la planta de tratamiento.
Fibrocemento (uralita)

Antes de proceder con la instalación de la cubierta, es necesario proceder a retirar la antigua, comprendiendo las placas de fibrocemento, cumbreras, caballetes, canalones ocultos y exteriores, impermeabilizaciones adheridas, laminas asfálticas, conductos de ventilación etc,. desescombro y transporte del mismo a contenedor a pie de calle y vaciado en vertedero autorizado , incluido parte proporcional de maquinaria auxiliar de obra, según NTE/ADD-3.
En el caso de los materiales que contengan amianto se actuará según Real Decreto 396/2006 (realización del Plan Específico de retirada de las placas de fibrocemento y aprobación por parte de la administración del mismo), incluyendo caseta de descontaminación
Si la cubierta tiene una estructura no aprovechable se procederá al cambio de la misma. Esta puede ser de diversos materiales, siendo los más habituales correas pretensadas de hormigón o bien estructura metálica ligera, y en algunos casos madera laminada estructural.
Viguetas pretensadas de hormigón

La primera opción es la colocación de viguetas pretensadas de hormigón prefabricado, colocadas sobre 2 vigas de carga centrales, en medidas aproximadas de 4,00 metros lineales por unidad y espaciadas entre ellas sobre 1,20 metros lineales. La vigueta más común a utilizar será la denominada T-14 cuyas medias se corresponde con una altura de 14 cm y utilizables hasta una longitud máxima de 6 m.
Estructura Metálica ligera
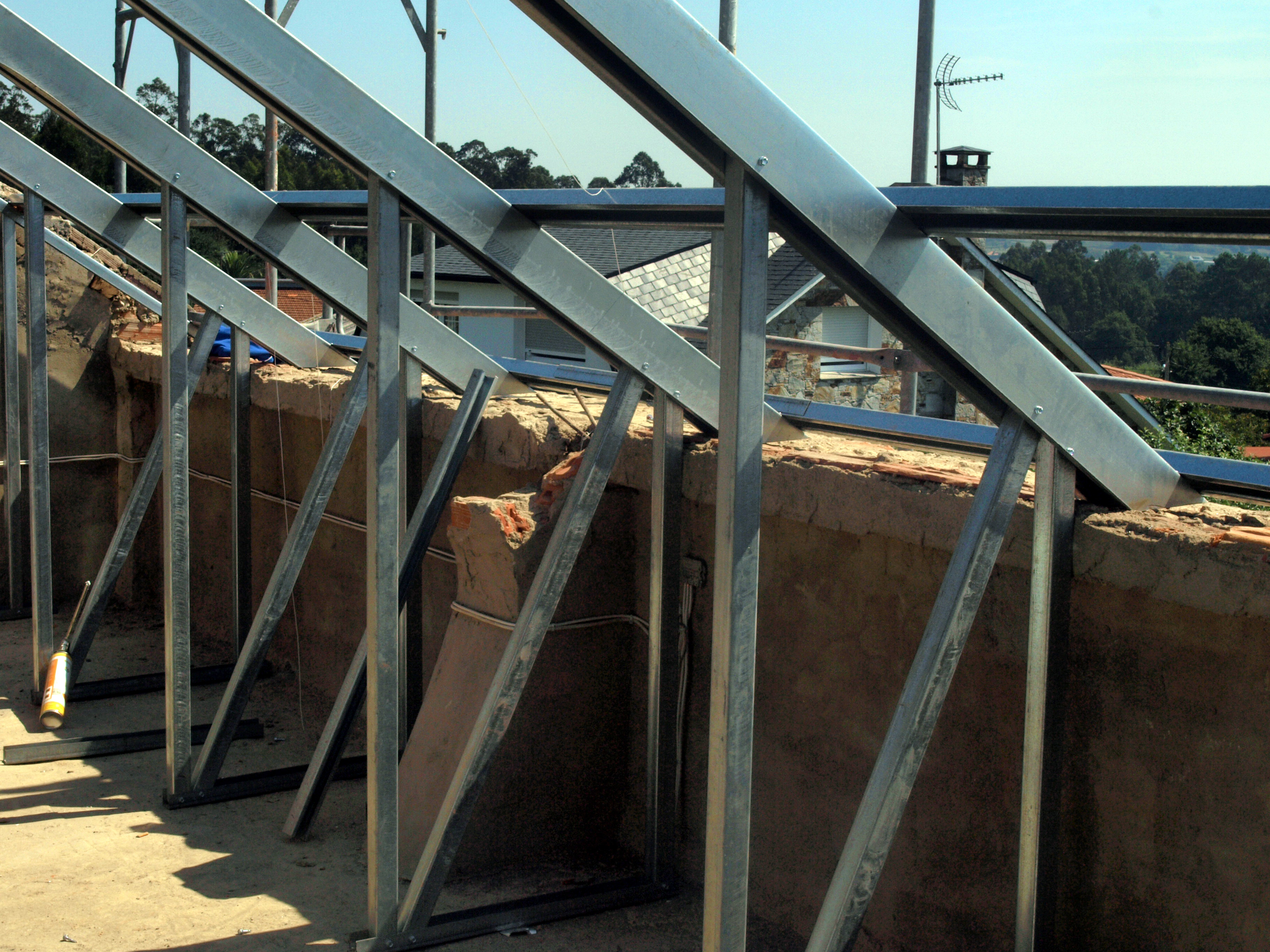
Otra opción es la colocación de una estructura metálica ligera galvanizada, como refuerzo de la actual, consistente en perfiles metálicos obtenidos por laminación en frío y tratados mediante un galvanizado. Todas las soluciones deberán ir atornilladas, nunca soldadas. La soldadura haría que desapareciese el galvanizado en esa zona y, por lo tanto, se correría el riesgo de ser atacado por agentes exteriores.
Aislamiento térmico
De forma opcional, antes de continuar con la colocación del fibrocemento, se puede proceder al aislamiento térmico de la cubierta.
Colocación de la nueva cubierta
Una vez todos los requisitos previos estén acabados se colocará una nueva cubierta, a base de placas de fibrocemento sin amianto, tipo gran onda, en color rojo, incluso parte proporcional de solapes, piezas especiales de remate, tornillos o ganchos de fijación, juntas ... etc. y medios auxiliares.
Esta es una solución de cubierta en forma de placa, fabricada en fibrocemento de 6,5 mm de espesor, cuya sección transversal está formada por ondas regulares que mejoran notablemente su resistencia mecánica y canalizan la evacuación de aguas pluviales. Incorpora además un fleje de seguridad de polipropileno en cada una de las ondas.
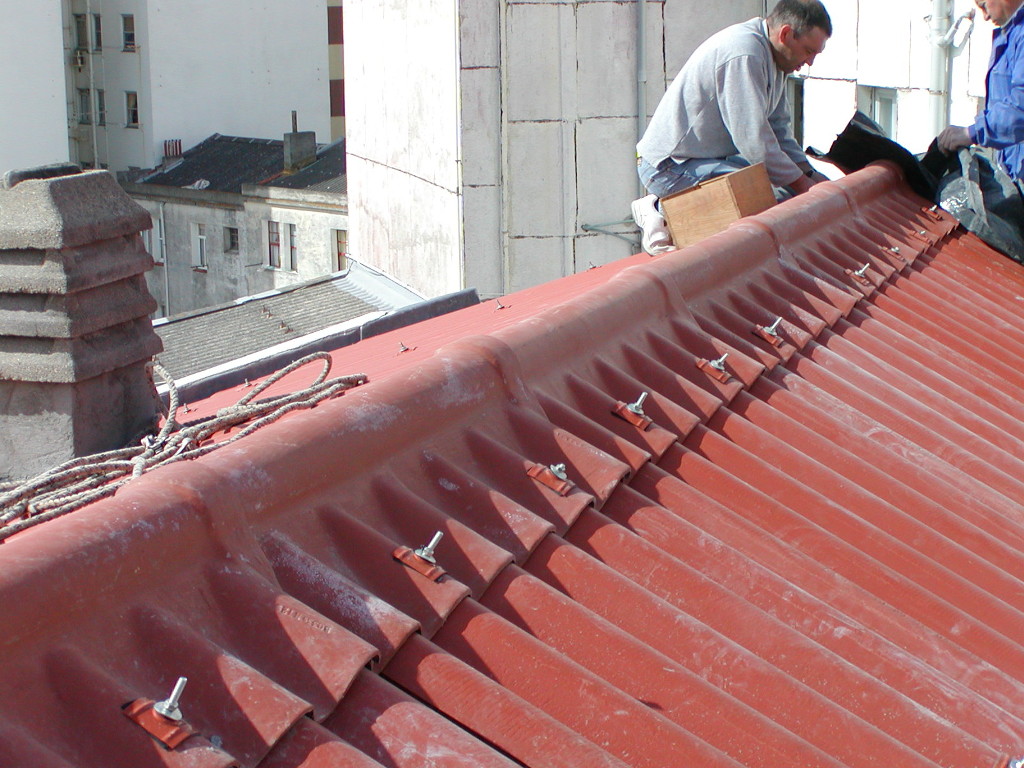
Las características técnicas habituales de este tipo de materiales son:
- Tipo de onda 177 x 51
- 2832-08 de ondas 6 ondas
- Ancho 1095mm
- Espesor nominal 6.5mm
- Densidad 1350kg/m3
- Reacción al fuego M0
- Garantía 10 años
Finalmente se procederá a la colocación de cumbreras y remates que garantizan el acabado final perfecto e impermeable de la cubierta.
Este sistema cuenta con 10 años de garantía. Es posible colocar teja como elemento de cobertura final, lo que ademas de darle un acabado más noble ampliaría la garantía a 35 años.
Teja
Rehabilitación de una cubierta de teja
Uno de los principales problemas de las cubiertas de teja antiguas es un problema de desplazamiento o corrimiento de la misma lo cual genera un problema de seguridad ya que con vientos fuertes (incluso medianos), pueden volar o desprenderse y caer sobre la calle con el grave riesgo que esto conlleva.

Otro de los problemas y también en un porcentaje altísimo es que se encuentran descascarilladas, es decir, vulgarmente peladas. Este fenómeno se manifiesta por la climatología y por el sistema en que fue colocada la cubierta en su origen, con morteros.
Hoy en día, las cubiertas, se ejecutan mediante atornillado cada “x” filas, se pegan con espuma especial de poliuretano, se colocan con gancho de acero inoxidable, es decir, montando una cubierta en seco y totalmente ventilada. Y se insiste en este sistema, por parte de los fabricantes, ya que la vida útil de una cubierta se basa en su auto ventilación y elementos que permitan su transpiración, es decir, colocadas en seco y pegadas con espuma.
Los agentes climatológicos como lluvia, sumados a ciclos de temperaturas extremas (heladas nocturnas y sol por las mañanas), hace que el pegote de masa de cola o cemento no deje transpirar a la teja y esta con los ciclos de hielo/deshielo se desconche, especialmente en los faldones con orientación norte. El motivo de los desprendimientos es la nula fijación de las mismas al soporte de fibrocemento y entre ellas. Esto es motivado, por una práctica habitual hasta hace unos años, en el que las tejas se fijaban con morteros o cementos colas que con el paso del tiempo y la climatología se despegaban o incluso rompían, agravado además, por la falta de ganchos en su colocación.

Actualmente estos sistemas de colocación han sido sustituidos por una colocación basada en la fijación mediante espuma de poliuretano, colocación de ganchos en inox entre ellas y la fijación mecánica de hiladas (con tornillo) cada ciertos tramos de acuerdo al porcentaje de pendiente.
Estos sistemas actuales, han sido desarrollados y comprobados en laboratorio, con resultados más que satisfactorios, obteniendo homologaciones diversas, pudiéndose dar una garantía por parte del fabricante y por parte del instalador de 35 años. Esto es importante, ya que muchas veces, algunos instaladores pueden ofrecer una garantía que no es respaldada por el fabricante. Nuestro consejo como instaladores, es que elijan no solo la mejor oferta económica, si no aquella que por sus materiales ofrece mayor garantía.
Nuestro trabajos se realizan siempre siguiendo un sistema patentado y con certificación del fabricante. Es una solución integral que contiene todos los elementos necesarios para realizar la instalación de un tejado de estructura de cubierta diseñada para la colocación de teja: forjado inclinado cerámico o de hormigón, tabiques palomeros y viguetas metálicas, estructura de madera,... etc. La pendiente mínima para la aplicación de este sistema es de 15% hasta parámetros verticales.
Este sistema permite dar garantía a la cubierta de hasta 35 años.
Para poder dar esta garantía de 35 años, es necesario retirar la totalidad de las tejas de cubierta, ya que ningún fabricante de tejas podrá darles una garantía sobre una cubierta que no está fabricada por él. Nos ceñimos a un Documento de idoneidad técnica (DIT) otorgado por el Instituto de ciencias de la construcción Eduardo Torrojas de Madrid.
Además la teja que colocamos siempre cumple con las normas UNE EN1304, EN1024, EN538, EN 539-1 y EN539-2 con certificado AENOR nº 034/000583.
CUBRICIÓN EN TEJA CURVA DE UNA CUBIERTA DE FIBROCEMENTO

La cobertura de una cubierta de fibrocemento, además de incrementar las ventajas técnicas, impermeables y estéticas de la misma, nos permite aumentar la garantía de la cubierta, pasando de 10 a 35 años.
Este incremento viene otorgado por parte del fabricante de la teja, ya que se realiza siguiendo los pasos referenciados en un Documento de idoneidad técnica (DIT) patentado y certificado por el fabricante.
Se realiza una cobertura del fibrocemento mediante la colocación de teja curva, colocadas por hileras paralelas al alero, asentadas con espuma de poliuretano incluyendo la parte proporcional de piezas especiales de remates y cumbreras.
Este sistema es el fruto de un proceso de investigación y diseño dirigido a conseguir un producto con una resistencia excepcional a heladas. El resultado supera ampliamente el mínimo exigido por la Unión Europea.

La fijación de las tejas en el faldón se realiza con ganchos y puntos de espuma de poliuretano. Los canales de la placa de fibrocemento deben quedar siempre libres.
En las zonas singulares como alero y remates laterales se fija además con un tornillo placa metal a la onda alta de la placa de fibrocemento. En función de la longitud del faldón y la pendiente del mismo, se atornilla, además, algunas filas utilizando la teja taladrada de acuerdo a la siguiente tabla.
Pendiente (%) | Nivel de fijación |
> 50 | 1 hilada cada 6 |
> 70 | 1 hilada cada 4 |
> 100 | 1 hilada cada 2 |
> 150 | Todas las hiladas |
Se colocan las primeras tejas canal a lo largo del alero, fijándolas con dos cordones de espuma de poliuretano aplicados sobre los laterales de la teja, y empleando un cordel para asegurar su alineación.
A continuación se van colocando las tejas cobija, empleando las tejas de alero (precortadas y taladradas).
Para ello, se termina de partir el trozo de teja precortado y se suplementá en la boca ancha para mantener la misma pendiente del resto de las hiladas del faldón. Esta teja se fija con espuma y un tornillo placa-metal a la placa de fibrocemento.

Las líneas de borde lateral se ejecutan con tejas de remate lateral, que se atornillan a la placa de fibrocemento además de fijarse con espuma. Para que la separación del goterón sea entre 2 y 5 cm.
Para la colocación de las piezas de remate lateral debe tenerse en cuenta en el momento del replanteo de la placa de fibrocemento para terminar con el final de la onda a 4-7 cm de la pared lateral terminada.
En la realización de la línea de cumbrera es necesario colocar las tejas de cumbrera en función de las lluvias y vientos dominantes. La cumbrera se resuelve con una perfilería metálica compuesta por:
- Pletinas de acero que van atornilladas a la onda alta de la placa de fibrocemento. La cantidad de pletinas es de 1 cada 6 ondas.
- Varillas de acero de métrica 8 mm, que roscadas a las pletinas anteriores sujetan el perfil de cumbrera permitiendo su regulación en altura.
- Perfil de acero galvanizado sobre el que se atornillan las tejas de cumbrera.

Una vez colocada las pletinas de sujeción de la perfilería de cumbrera, se presentan todas las tejas canal de la última hilada horizontal superior por ambos faldones y se coloca la lámina impermeable transpirable de modo que queda sujeta por estas tejas. A continuación se colocan todas las tejas cobija de la última hilada, fijándolas con espuma.
Para garantizar una correcta evacuación del agua de la cumbrera se coloca una cuña en cada canal. Se colocan las varillas de M8 que sujetan el perfil longitudinal de cumbrera atornillándolas a las pletinas de acero. Para garantizar la perfecta nivelación del perfil, se tiende un cordón entre la parte superior de la primera varilla de la línea de cumbrera y la última.
Se coloca el perfil de cumbrera y se fija mediante tuercas a las varillas M8. Finalmente se colocan las tejas de cumbrera fijándolas al perfil, junto con la grapa que sujeta una teja con la siguiente, mediante un tornillo auto taladrante y un cordón de espuma.
Detalles singulares y ejemplos gráficos:
Metalicas de panel sandwich
Esta es una solución ligera en cuanto a peso, y su resultado es muy bueno. Una ventaja importante de este sistema es que las planchas son enteras de arriba abajo, con lo cual no hay juntas intermedias, salvo en los solapes entre ambas. Permite además ofrecer 10 años de garantía.
Normalmente es necesario realizar una sustitución total de la cubierta, con la retirada de la anteior. Teniendo en cuenta cuando fuera aplicable la normativa de materiales peligrosos por contenido en amianto.
La cubierta consiste en panel sándwich de chapa en ambas caras con un núcleo central de poliuretano de 4 a 6 cm que hace a su vez de aislamiento térmico.
Los trabajos constan de las siguientes fases:
SISTEMAS DE ELEVACIÓN MEDIANTE CAMIÓN AUTO GRÚA.
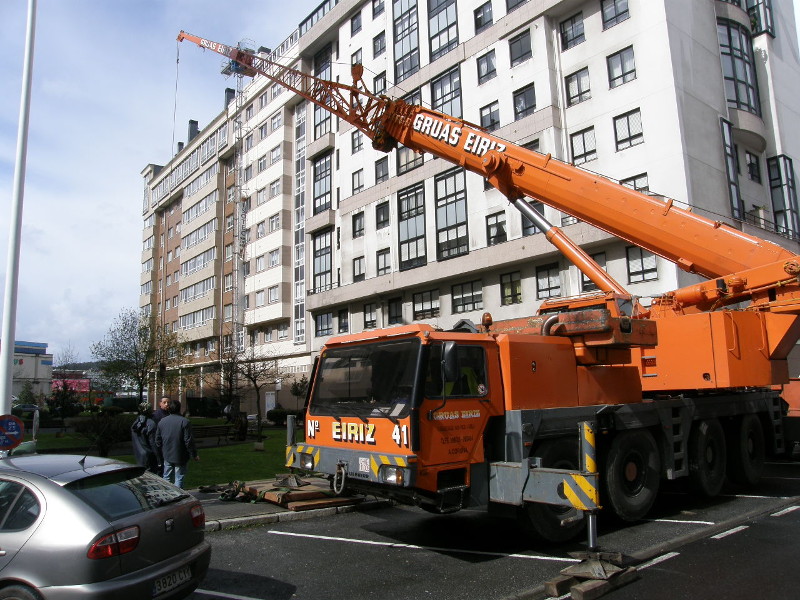
Siempre que sea posible, dado que acorta enormemento los plazos de ejecución se alquila durante el tiempo necesario un camión auto grúa, con brazo hidráulico con alcance hasta 36/45 metros para el suministro de materiales a cubierta, así como para la retirada de las materiales desmontados y depositarlos a pié de calle debidamente embalados y flejados según normativa.
En el caso de no poder realizarse los trabajos con camión grúa se utiliza un montacargas homologado para la subida y bajada de materiales, así como de personas.
LINEA DE VIDA PROVISIONAL
Cumpliendo las normativas de seguridad se instala una de línea de vida provisional, mediante cable de acero, incluyendo uniones y anclajes a zonas sólidas de la cubierta. Dichas líneas de vida, se usarán para que el personal que esté trabajando en la cubierta se enganche el arnés de seguridad a ella.
DESMONTADO y RECICLADO (DESAMIANTADO) DE CUBIERTA: PLACAS DE FIBROCEMENTO, CABALLETES, PIEZAS DE REMATES, ETC.,
Se procede al desmontado de la cubierta, comprendiendo las placas de fibrocemento, cumbreras, caballetes, impermeabilizaciones adheridas, laminas asfálticas, conductos de ventilación etc,. desescombrado y transporte del mismo a contenedor a pie de calle y vaciado en vertedero autorizado , usando maquinaria auxiliar de obra, según NTE/ADD-3.
En el caso de los materiales que contengan amianto se actuará según Real Decreto 396/2006 (realización del Plan Especifico de retirada de las placas de fibrocemento y aprobación por parte de la administración del mismo).
TRANSPORTE A VERTEDERO DE ESCOMBROS
Se Transporta los escombros generados en obra, (sin incluir las planchas de fibrocemento con amianto retiradas) a un vertedero autorizado con gestión de residuos cumpliendo con todas las medidas de seguridad y salud.
COLOCACIÓN DE LA CHAPA DE CUBIERTA
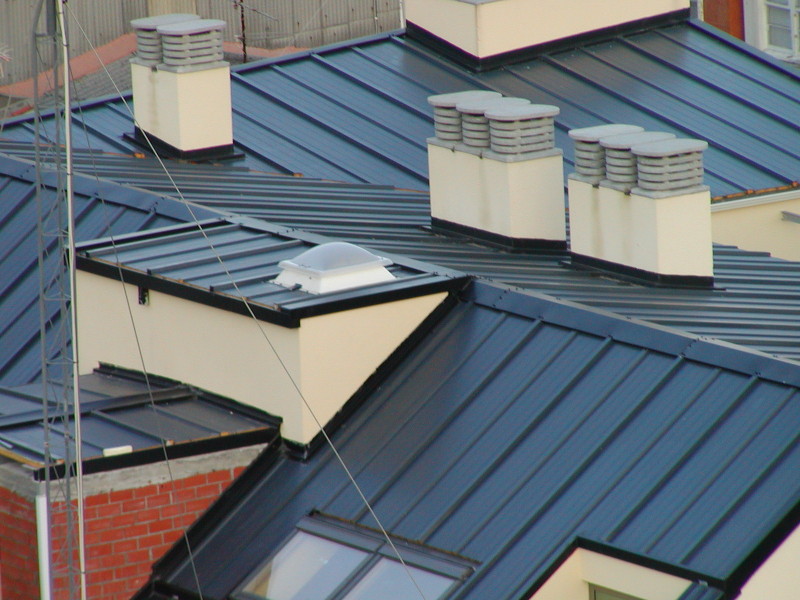
El siguiente paso es proceder a instalar la cubierta de panel de chapa sándwich en color. Siendo rojo o negro los más habituales, aunque existe una amplia gama de colores para elegir.
Esta es una cubierta formada por panel de chapa de acero galvanizado de 0,6 mm prelacada en la parte exterior, una chapa de acero galvanizada en la parte interior de 0,6 mm, y un núcleo de espuma de poliuretano de 4 cm, densidad de 40 kg/m3 instalada sobre la estructura de correas existente y sujeta con tornillería estanca.
Trambien se realizá una colocación de cumbreras , limas, remates perimetrales de petos en chapa lis, conformada prelacada de 0,6 mm de espesor y diámetro máximo de 750 mm, colocación de boquillas para entronque con bajantes del mismo color y referencia "Ral", que la cubierta, atornillado con tornillería de aluminio con junta estanca. Totalmente terminada.
CANALÓN – LIMAHOYAS y REMATES
Normalmente es neceraia la colocación de unos nuevos canalones de chapa de acero prelacado hasta entronque el de las bajantes anteriores.

Tambien en esta fase se procedera a colocar:
- Limahoyas interiores.
- Remates angulares vierteaguas sobre limahoya en acero prelacado.
- Remates varios de cubierta en chapa de acero prelacado.
- Remates laterales.
- Etc.
COLOCACIÓN DE CLARABOYAS DE SALIDA COMUNITARIA O LUCERA.
Finalmente si procede se realiza la instalación de claraboyas o luceras de poliéster.
Aislamiento térmico de cubiertas
La necesidad de aislar térmicamente el tejado de la casa se hace especialmente patente al considerarlo como su fachada más expuesta, tanto en condiciones invernales como, con mayor relieve incluso, en condiciones estivales: esto es así por efecto de la radiación solar, que tiene la consecuencia de que la temperatura superficial de los materiales de acabado -tejas- es superior a la temperatura del aire exterior, del orden de 15 °C mas (35 °C del aire exterior,p.ej., y 50 °C de la teja). Por tanto el salto térmico real es, no de 35 - 25 (temperatura interior) = 10 °C, sino de 50 - 25 = 25 °C. Y las ganancias de calor por transmisión térmica dependen proporcionalmente de ese salto real. (Por supuesto la temperatura del material de acabado puede ser aun mayor con colores oscuros o negros como es el caso del fibrocemento).
Para aislar una cubierta hay diversas opciones, las más usadas es la colocación de manta o plancha de aislamiento, o un proyectado de poliuretano, de las que destacamos las dos que consideramos más adecuadas.

Manta de aislamiento térmico
Esta opción se trata de la colocación de una manta de aislamiento térmico en lana de roca no revestida de un mínimo 4 cm de espesor, para disponer sobre el falso techo de las viviendas sobre las que se ubica la cubierta.
El material a usar consiste en paneles semi-rígidos de lana de roca no revestido, con objeto de colocarlos sobre el falso techo desde la zona superior; de manera que se adapten a la geometría del entramado soporte existente.
Planchas de poliestireno extrusionado

Esta otra opción se trata de la colocación de planchas de aislamiento térmico de poliestireno extrusionado de un mínimo de 4 cm de espesor, especial para cubiertas.
Este sistema consta de la instalación de planchas rígidas de espuma de poliestireno extruído (XPS) con estructura de célula cerrada. Estas planchas son altamente resistentes a la absorción de agua y su capilaridad es nula. Además también son muy resistentes a la difusión del vapor de agua y no se ven afectadas por ciclos repetidos de congelación-descongelación.
En estos materiales no se desarrolla el moho. Y no tienen valor nutritivo para roedores, insectos, etc.
Adecuadamente instaladas, se estima como vida de servicio de las planchas es la misma que la del la del resto de la construcción o estructura edilicia en que se integren.
Cubiertas de PVC
Los problemas más comunes de la cubiertas realizadas en PVC son los siguientes:

- La lámina ha perdido su plastificante, ya que con la radiación solar pierde todas sus propiedades, decolorándose, dejando la armadura al aire y generando debilitamiento y rigidez de la misma.
- La armadura de la lámina es de fibra de vidrio. Las láminas de PVC realizadas con armadura de fibra de vidrio, no son válidas para ir con fijación mecánica por las tensiones a las que es sometida y solamente son válidas para ir adherida totalmente al soporte con cola de contacto especial.
- Las láminas que son validas para la fijación mecánica son las de armadura de Poliester.
- La lámina no está bien soldada o pegada, el aire entra y circula por debajo de la lámina, rasgándola en las zonas más debilitadas o en aquellas zonas donde está más tensionada.
- Excesivo tensionamiento de la lámina, por una mala práctica de instalación, en la que no se calculaban los puntos de tensionamiento y esta, se colocaba de manera continua, haciendo que en los cambios climatológicos, tensione y se destensione en función de la temperatura.
Todo este cúmulo de circunstancias genera que no sea posible reparar muchas veces la cubierta, ya que la lámina existente no permite parcheos ni admite las soldaduras de nuevas láminas por el envejecimiento de la misma. Si además ha perdido su capacidad impermeable o está en el límite de vida útil de la misma, esta se convertirá en débil y rígida.
Ejemplo gráfico y real (fotografías tomadas en obra) de cómo ha ido deteriorándose la una lámina con el paso del tiempo:

- 1.- Estado más o menos original de la lámina. Situado en una zona sombría. No ha perdido ni el plastificante ni el color.
- 2.- La lámina empieza a perder por zonas el plastificante, formando aguas en su composición.
- 3.- Perdida total del plastificante y del color. Empieza a ser visible la armadura.
- 4.- Comienza a asomar la fibra de vidrio que sirve de armadura a la lámina de PVC.
- 5.- Estado generalizado en las zonas de sol. Pérdida total del plastificante y con toda la armadura en superficie al descubierto.
Proceso de reparación de cubierta PVC
Se coloca, en la totalidad de la cubierta, una nueva lámina de PVC por encima de la actual. No procedemos a eliminar la existente, ya que se mantiene sirviéndonos como base, cortándola en las zonas de tensión que sea necesario, fijándola mecánicamente de nuevo. Para acabar se coloca en su totalidad una nueva lámina de PVC (pero con armadura de poliéster) por encima de la vieja. Previamente a la colocación se colocará una lámina de geotextil como barrera de vapor y/o capa separadora.
En algunos casos, será necesario retirar la totalidad de la lámina existente.
A continuación detallamos los pasos a seguir en la reparación o rehabilitación de una cubierta tipo PVC:
SUSTITUCIÓN / REPARACIÓN DE REVESTIMIENTO EN MAL ESTADO
Donde fuese necesario, se procederá a la sustitución de aquellas zonas de revestimiento que ese encuentre deterioradas, tensionados, rasgadas, sueltas o en mal estado, por una nuevas de las mismas características que la que tiene actualmente.
Se cortará las zonas en mal estado o tensionadas, para colocar unas piezas nuevas independientes, que impidan que estas se vuelvan a tensionar.
DESMONTAJE DE ANGULARES
Se procede al desmontaje de todos los angulares actuales de la cubierta, y en especial aquellos que se encuentran en la zona de los canalones que habitualmente son los que están dañados.
CAPA SEPARADORA: MEMBRANA DE GEOTEXTIL

Se coloca de una membrana de Geotextil , como base protectora y capa separadora de la lámina impermeabilizante.
Es un Geotextil no tejido termosoldado a base de polipropileno para construcción y obra civil.
Usando su permeabilidad transversal, nos permite el paso del agua para su conducción, reteniendo las partículas finas del suelo lo que se logra según el tamaño del poro.
Evita la mezcla de partículas de suelos distintos. Impide el contacto entre materiales no compatibles. Barrera permeable entre suelos de distinta estructura.
COLOCACIÓN DE PLANCHAS AISLANTES DE 4 CM.

Seguidamente se procede a colocar planchas aislantes de poliestireno extrusionado de al menos 4 cm. de espesor (XPS). Este aislamiento térmico se le considera el más idóneo para este tipo de obra por su resistencia a la humedad, sus excelentes propiedades como aislamiento térmico, por su alta resistencia al paso de vapor de agua, capilaridad nula, duración y que es además ignífugo. Son planchas rígidas de espuma de poliestireno extruido con estructura de célula cerrada.
Las planchas de poliestireno extrusionado son altamente resistentes a la absorción de agua y su capilaridad es nula. Las planchas XPS son muy resistentes a la difusión del vapor de agua y no se ven afectadas por ciclos repetidos de congelación-descongelación. En las planchas de poliestireno no se desarrolla el moho. No tienen valor nutritivo para roedores, insectos, etc.
Adecuadamente instaladas, se estima como vida de servicio de las planchas la del resto de la construcción o estructura edilicia en que se integren.
Propiedades
- Excelente conductividad térmica (λ)
- Gran resistencia a la compresión y a la fluencia (deformación por compresión a largo plazo).
- Célula cerrada: absorción de agua despreciable y alta resistencia a la difusión del vapor (factor μ)
- Alta resistencia los ciclos de hielo-deshielo.
- Insensibilidad a la humedad, a corto y largo plazo. Capilaridad nula.
- Resistente al envejecimiento.
- Clasificación M1 de reacción al fuego y Euroclase E.
Se colocan las planchas encajadas unas con otras sobre la impermeabilización anterior existente.
La impermeabilización queda completamente protegida, tanto térmica como mecánicamente, prolongando la durabilidad de la misma.
No es necesaria la barrera de vapor, ya que la impermeabilización tiene esta doble función por estar colocada debajo del aislamiento.
COLOCACIÓN DE ANGULARES DE CHAPA GALVANIZADA COLAMINADOS CON PVC.
El siguiente paso es colocar angulares de chapa galvanizada colaminados con PVC, fijados mecánicamente al soporte y sellados con masilla de poliuretano, en todo el perímetro de la cubierta a excepción de los de fachada principal.
COLOCACIÓN DE LAMINA DE PVC 1,5 FIJADA MECANICAMENTE
Finalmente se procede a colocar una lámina de PVC de 1,5 mm. de espesor, con armadura central en poliéster, fijada mecánicamente. La lámina a colocar será de reconocido prestigio y altas prestaciones (no utilizamos láminas de segundas calidades). Todas tienen todas las certificaciones AENOR y CE.
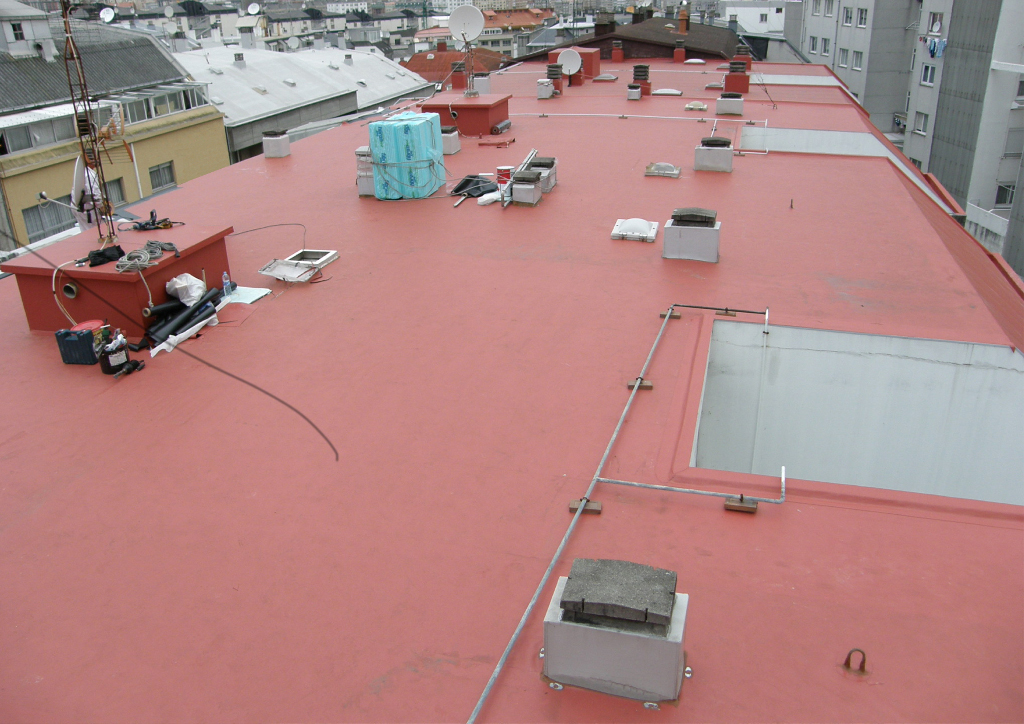
El color a utilizar será gris claro, gris oscuro, rojo o verde como tonos más habituales y el alcance de los trabajos comprende normalmente la totalidad de la cubierta del edifico, incluyendo vueltas sobre fustes de chimeneas, muretes de separación, remates, canalones, etc. para que quede una cubierta completamente estanca y sin humedades ni filtraciones de agua.
En las zonas verticales de chimeneas, así como en los casetones, habrá que eliminar la totalidad de la existente para colocar una nueva, pero encolada con cola especial, ya que no puede hacerse mediante fijación mecánica.
La fijación mecánica se realizará con espigas fabricada con polipropileno y clavo expansionante con aro de estanquidad.
Propiedades:
- No se oxida.
- Con clavo expansionante que asegura la fijación.
- Dos longitudes de espiga con el mismo diámetro.